Black Gold in Brockham
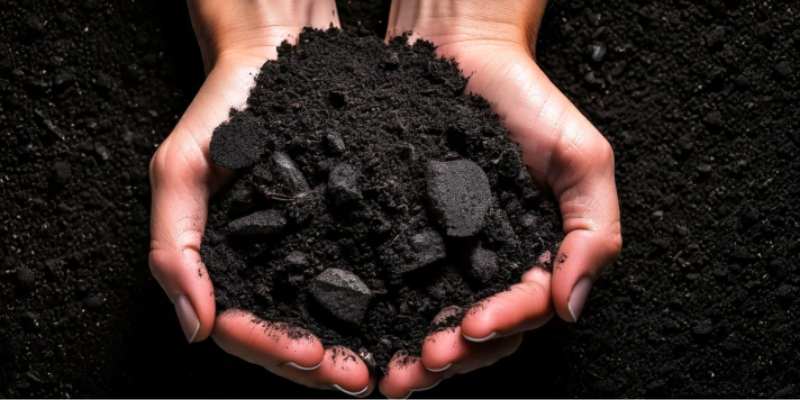
An inspiring story of finding value in a by-product – and reducing carbon emissions
We have plenty of trees in Betchworth, but surely not enough to explain the number of tree surgeons’ trucks that pass through the village or along the A25 each afternoon - trucks full of chipped-up branches and smaller limbs from their day’s work.
The explanation...most are heading for the communal chip yard in Old School Lane, Brockham.
Until recently the 8-9,000 tons of woodchip deposited each year at Felton’s Farm were re-loaded onto immense lorries and taken to the North of England or deepest Kent as fuel for biomass-based power plants. But now, after the Brodies secured a multi-million ‘green loan’ from HSBC, around half of this once low-value by-product is being converted to Biochar, a carbon-rich high-value soil improver. Most of the remaining chips are material for a large-scale composting operation.
What is Biochar?
At first sight biochar looks like very small sized charcoal but it is much more porous and so has a larger surface area - a kilogram of it will have a surface area of several football fields. When spread on agricultural land, studies have shown that biochar improves soil structure, aids water retention in dry periods, provides a habitat for beneficial soil microbes and plays a crucial role in nutrient cycling and promoting plant growth. Over time it reduces reliance on chemical fertilisers and pesticides.
How is it produced?
At Felton’s Farm the leaves and small twigs in the chippings are screened out and taken to large compost windrows. The remaining chips are dried, reducing the weight by 30%. Oversize chips are then blown aside and sold on for use in landscaping, animal bedding and biomass boilers.
What’s left – some 2,500-3,000 tons a year – is fed into a space-age pyrolysis unit which runs 24/7, ‘firing’ the chips then moving them to continue the transformation in a low oxygen chamber before they fall into a quenching unit and emerge as some 900tons of high-value biochar each year.
The pyrolysis unit was developed and built in Wales by Woodtek, the company of farmer turned engineer Mick Jones. You can read their fascinating story here.
Self-sufficient production
The excess heat generated is recycled back to the start to dry the wood chippings, as well as drying crops in season. In time, with investment in some additional kit, the excess energy will be fed back into the National Grid.
In other words, once the process is started, all the team at Feltons Farm have to do (as if!) is feed the newly arrived woodchip into the system, and the system provides the energy and heat to run itself.
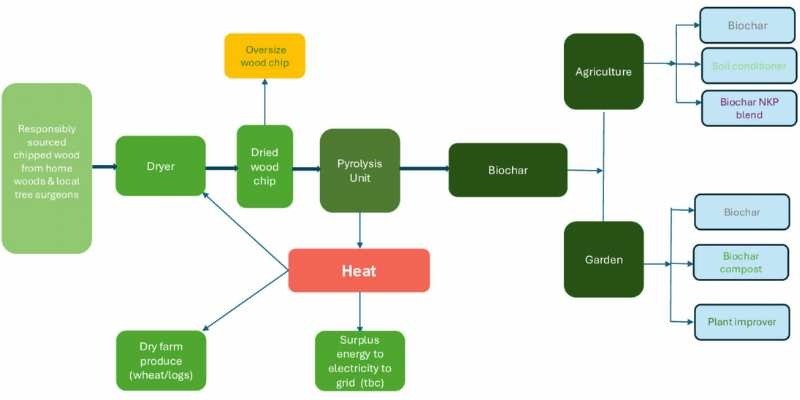
And that’s not all! There’s the compost too.
The fines (small twigs and leaves) removed from chippings are mixed with various manures from the farm along with the biochar and composted in huge windrows. Each batch is monitored and recorded, focusing on moisture, oxygen content and temperature, crucial for the activity of beneficial microbes, nematodes, and fungi.
After six to twelve weeks, depending on conditions, large volumes of high-quality compost are available for use on Felton’s Farm itself as they head down the regenerative farming route, and for big landscaping projects.
As production increases, this high quality, peat-free compost made entirely from local ‘waste’ materials will be available through a retail operation, as will the Biochar and dried woodchip.
You can read much more about the whole fascinating process at Brodiebiomass.co.uk
The Brodies also retail the compost, biochar and landscaping woodchip in season through http://www.soilfixer.co.uk